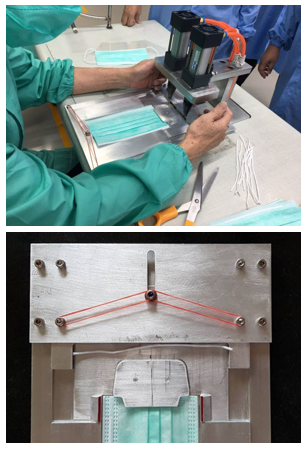
A team of KMUTT researchers has teamed up with Thai Hospital Products Co., Ltd. to accelerate production for ensuring Thai people sufficient supply. The team has 4 members leading by Assoc. Prof. Dr. Bavornchok Poopat and Mr. Nopnarong Sirisatien, KMUTT lecturers at the Department of Production Engineering. Secondly, Mr. Paisal Tangchaisin is a former student of the Department of Production Engineering. Lastly, Mr. Thossaporn Bunthae is from The Institute of Field Robotics (FIBO).
Assoc. Prof. Dr. Bovornchok Poopat revealed the plan after working with the company to help plan and design special equipment to increase their output. Because of the uninterrupted production, the company runs its automatic machines, a semi-automatic machine, and 60 manual ultrasonic welding machines in 2 shifts to raise the output. The limitation of time for maintenance leads the team to work on the development of 60 manual ultrasonic welding machines rather than the automated machines which cannot afford interruption to make the least effect on the current production plan.
Workers have to manually feed ear loops into a manual ultrasonic welding machine and weld them together with a face mask which slows the process and requires certain skills. The skillful workers can have 4,800 pcs/8 hours while less skilled or new workers can produce only 1,200-2,000 pcs/8 hours and the quality has not been consistent. After the team helps the company to change the working procedure for the workers and install additional equipment, a new ultrasonic welder head, the production can be raised to 5,000-6,000 pcs/ 8 hours or a 50% growth of production capacity. If the prototype is fully developed, the output can be increased to 6,000-6,5000 pcs/machine/8hrs or 360,000-390,000 pcs/60 machines/8hrs. Besides, the total capacity of the new machine combines with both automatic and semi-automatic machines will be 30% higher.
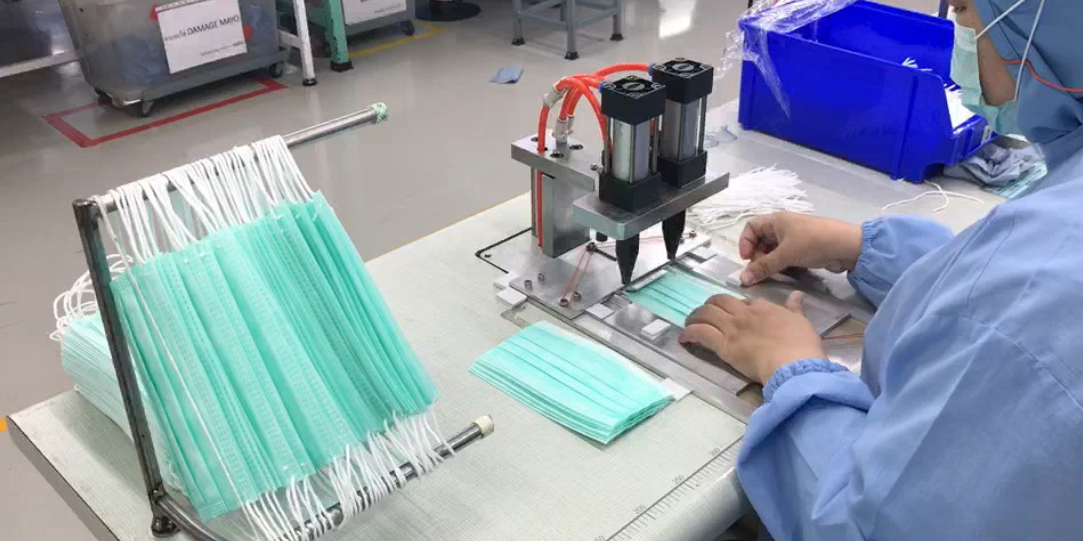